Roman Schwörer
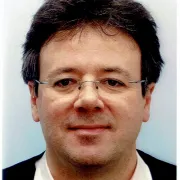
Effizient planen, bauen, umbauen und renovieren
Ich bin Ingenieur und Energieberater aus Leidenschaft, da sich dieser Beruf durch eine immens große Vielfalt auszeichnet. Ob Kostenkalkulation, Kostenschätzung oder -berechnung, Unterstützung bei der Beantragung von Fördermitteln, Ausschreibung von Handwerkerleistungen, Termin- und Qualitätsüberwachung oder Energieeinsparung durch Prozess-Optimierung und/oder Optimierung einer Gebäudehülle – bei alledem kann ich meine detaillierten Fachkenntnisse voll ausschöpfen, um nachhaltige Ergebnisse zu erzielen.
Abwärmenutzung an fünf installierten Druckluftkompressoren.
Davon zwei baugleiche mit je 90 kW elektrischer Leistung und konstanter Drehzahl, zwei mit 132 kW und konstanter Drehzahl und ein weiterer Kompressor mit variabler Drehzahl und Leistung bis 160 kW. Durch den fünften, variablen Kompressor kann die Erzeugung an den jeweiligen Bedarf angepasst werden.
Die vier baugleichen Druckluftkompressoren sind mit je einem Wärmetauscher ausgestattet, um die Abwärmenutzung und Heizungsunterstützung zu ermöglichen.
Die theoretisch entstehende Wärmemenge der Kompressoren ermittelt sich wie folgt:
Die 90 kW-Kompressoren erzeugen je 66 kW Wärmeenergie. Gerechnet wird aber nur 1 Kompressor.
Die 132 kW-Kompressoren je 99 kW. Auch hier kann aufgrund der fehlenden Gleichzeitigkeit nur 1 Kompressor gerechnet werden.
Die Druckluft wird an 365 Tagen, 24 Stunden aufrecht erhalten.
Für die Berechnungen geht man davon aus, dass die zur Verfügung stehende Wärmemenge nur zu maximal 90% genutzt werden kann. Es ergibt sich eine zur Verfügung stehende Wärmemenge von 365 Tage x 24 Stunden x 90% x 165 kW = ca. 1.300 MWh/anno. Darüber hinaus müssen Speicher- (4 kWh/d) und Rohrleitungsverluste (36 kWh/d) abgezogen werden (kumuliert 350 MWh/a). Außerdem müssen die jahreszeitlichen Schwankungen des Wärmebedarf mit weiteren ca. 350 MWh/a. berücksichtigt werden.
Es verbleibt eine genutzte Wärmeenergie aus der Abwärme der Kompressoren in Höhe von 600 MWh (Einsparung)
Die Hilfsenergie (15 MWh/a.) zum Betrieb der Pumpen muss noch gegen gerechnet werden, da diese nur zur Nutzung der Abwärme erforderlich sind.
Die zu ersetzenden Kunststoff-Spritzgussmaschine hat eine Schließkraft der Maschine beträgt 80 to, welche vollhydraulisch aufgebracht wird. Ca. 12 kg thermoplastischer Kunststoff werden in der Stunde auf dieser Maschine verarbeitet. Der Kunststoff wird zunächst auf eine Verarbeitungstemperatur von ca. 230°C im Extruder erhitzt und plastifziert, um dann über eine Düse in das Formwerkzeug gespritzt zu werden. Das Formwerkzeug befindet sich in der vollhydraulischen Schließeinheit, welche mit großen Schließkräften für die Genauigkeit und Qualität der Endprodukte sorgt.
Die hydraulische Anlage besteht aus einer Formschlusshydraulik, die einen "großen" Weg mit kleiner Kraft und einer Zuhaltehydraulik, die nur einen kleinen Weg mit großer Kraft zurücklegen muss. Der Betrieb der Hydraulik ist mit einem hohen Lärmpegel und einem hohen Energie- und Kühlwasserbedarf verbunden, da die Hydraulik dauerhaft auf großen Drücken gehalten werden muss. Folglich sind leider auch hohe Öl-Leckagen vorhanden.
Der gesamte Energiebedarf zum Betrieb der Maschine setzt sich aus den Antriebsleistungen für die erforderlichen Hydraulikpumpen und vorhandenen elektrische Motoren sowie der erforderlichen Heiz- und Kühlaggregate für folgende Arbeitsprozesse zusammen: Zuführen, Plastifizieren, Einspritzen, Kühlen, Verschließen, Halten, Auswerfen.
Die zuvor beschriebene vollhydraulische Maschine soll durch eine neue, vollelektrische Kunststoff-Spritzgußmaschine ersetzt werden. Die erhebliche Energieeinsparung wird dabei in erster Linie bei der Schließeinheit durch den Verzicht auf Hydraulik und den Einsatz eines sogenannten Kniehebelssystems erreicht. Die verbesserte Heizbandisolierung der Plastifiziereinheit leistet einen weiteren wesentlichen Beitrag zur Minimierung des Energieverbrauchs. Vollelektrische Maschinen sind grundsätzlich leiser, energiesparender und sauberer, da kein Hydrauliköl benötigt wird.
Zur Beurteilung der Wirtschaftlichkeit eines gefertigten Teils dient der Energieeffizienzkoeffizient, der angibt, wie viel Energie pro Kilogramm verarbeiteter Masse benötigt wird. Für die neue Maschine wird vom Hersteller dieser Koeffizient mit 0,24 kWh/kg angegeben. Damit kann die Maschine in der höchsten Effizienzklasse 10+ nach Euromap 60-1 eingeordnet werden. Im Vergleich hierzu liegt die alte Maschine mit einer sehr geringen Energieeffizienz von vermutlich nicht weniger als 1,5 kWh/kg in der Effizienzklasse 2+.
- Fachingenieur:in Energieeffizienz
- BAFA Energieaudit EN 16247
- BAFA Energieberatung für Wohngebäude
- BAFA Energieberatung für Nichtwohngebäude, Anlagen und Systeme DIN V 18599
- BAFA Vor-Ort-Beratung
- BAFA Energieberatung im Mittelstand
- Förderung Energieeffizienz in der Wirtschaft (Anlagen und Prozesse)
- Förderung Energieeffizient Bauen und Sanieren Wohngebäude
- Förderung Energieeffizient Bauen und Sanieren Nichtwohngebäude
- Förderung Baudenkmale und erhaltenswerte Bausubstanz
- Förderung Barrierefreies Bauen und Wohnen
- PHI Passivhausberater:in
Architektur+Ingenieurbüro Schwörer
Schloßgasse 5
73453 Abtsgmünd
Deutschland
Für die Inhalte dieses Expertenprofils sowie die Einhaltung der Urheberrechte des Bildmaterials ist der Profilinhabende verantwortlich.