Frank Thurner
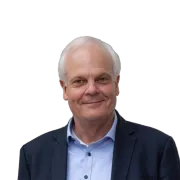
Ressourceneffizienz durch Robuste Produkte & Prozesse: Fehler, Ausschuss und Risiken vermeiden statt nacharbeiten, wegwerfen oder aus dem Feld zurückholen
Wir sorgen für robuste Produkte & Prozesse und sparen damit bis zu 60% Ressourcen ein. Den Bayerischen Ressourceneffizienzpreis 2021 hat unsere Schwesterfirma für die Ergebnisse erhalten, die wir gemeinsam mit unserer Methode Robust Design und ihrer Engineering-KI Analyser® für unsere Kunden erzielt haben.
Die mts Consulting & Engineering GmbH unterstützt Industrieunternehmen seit 2006 dabei, methodisch und nachhaltig robuste Produkte und stabile Prozesse zu implementieren. Wir decken die Ursachen von Kosten- und Qualitätsproblemen auf oder verhindern sie bereits im Vorfeld. Wir sichern die Produktfunktionalität und Industrialisierung ab und unterstützen Sie mit Predictive Analytics, Predictive Quality und Predictive Maintenance.
Ressourceneffizienz durch die Methode Robust Design, basierend auf Lean Six Sigma:
- Zusammen mit dem innovativen Engineering-KI-System Analyser® garantiert das Vorgehen nach Robust Design fehlerfreie Produkte & Prozesse.
- Robust Design ist in allen produzierenden Branchen bei kleinen und großen Stückzahlen anwendbar im gesamten Produktlebenszyklus vom Produktdesign über die Industrialisierung bis zur Serienproduktion und Wartung.
- Das Engineering-KI-System Analyser® funktioniert auch mit kleinen Anlernstichproben und verarbeitet neben Einzelwerten auch Kurven- und Flächendaten, was zu besseren Vorhersagemodellen führt.
Robust Design steigert die Ressourceneffizienz durch Fehlervermeidung in den Bereichen Ausschuss, Nacharbeit, Gewährleistungskosten und -risiken, Materialverbrauch, Produktions- und Energiekosten.
Robust Design und der Analyser® sind branchenübergreifend einsetzbar. Unser Schwerpunkt liegt im Automotive, Medizintechnik, Kunststofftechnik, Maschinenbau, Anlagenbau, Pharma und Chemie.
Für mehr als 60 Schraubverbindungen mittels Schraubkurvenanalyse (rein aus dem Verlauf Drehmoment vs. Winkel) die Fehler erkennen und abstellen, um Ausschuss und Gewährleistungsrisiken zu vermeiden.
Sprich Ressourceneffizienz durch vollautomatische Schraubkurven-Erkennung mit automatischer Erkennung der Fehlerbilder, Ursachen und Anzeigen der möglichen Maßnahmen und Lösungen, samt Handlungsempfehlung für die Umsetzung.
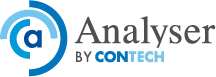
Die Herausforderung
Bei einem TIER 1 war die Rate der akustisch auffälligen Getriebe zu hoch. Es gab eine vierstellige Anzahl an möglichen Einflussgrößen. Mit ingenieursmäßigem Ansatz konnten die Ursachen der Akustik- und Geräuschprobleme daher nicht nachhaltig abgestellt werden.
Das Ziel
Mit möglichst wenigen Getrieben die Ursachen der Geräusch-, NVH- und akustischen Themen analysieren und nachhaltig beseitigen. Die Rückweise-Rate aufgrund von Akustik-Themen dauerhaft unter 0,8% senken.
Die Vorgehensweise
Mithilfe des KI-Systems Analyser®, das auch mit geringen Anlernstichproben auskommt, wurden anhand von ca. 25 Akustik-Mess-Kurven aus den Getriebeprüfständen die Ursachen und Wirkmechanismen aus den ca. 3.200 möglichen Einflussgrößen ermittelt.
Der Analyser® erstellte Vorhersagemodelle, mit denen die Geometrien der Zahnräder, Wellen, Spiele und Spaltmaße für die Akustik optimiert und das Best Setting errechnet werden konnten.
Ergebnis
250 T€
eingespart /Jahr
99,95%
Yield / Ausbringung
0,05%
Rückweise-Rate
Fallbeispiel als PDF downloaden
Die Lösung
Mit den vom Analyser® erstellten Vorhersagemodellen und den Best Settings wurden neue Nominalwerte für die wichtigen Einflussgrößen festgelegt und damit ein Bestätigungslos produziert. Die Akustik- und Geräusch-Themen verschwanden.
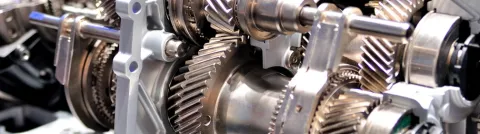
Die Herausforderung
In der Endmontage eines OEM verursachten hohe Fehlerraten pro Jahr siebenstellige Nacharbeitskosten inline und offline. Da es sich um täglich 280.000 sicherheitsrelevante Verbindungen pro Montagelinie handelte, konnten mit ingenieursmäßigem Ansatz die Ursachen nicht nachhaltig bearbeitet und abgestellt werden.
Das Ziel
Die Ursachen mit dem KI-System Analyser® analysieren und nachhaltig beseitigen und damit die Fehlerraten dauerhaft um 50 % senken.
Die Vorgehensweise
Zuerst wurden systematisch die Top Schraubfälle, die 50% der Kosten verursachten, aus den ca. 40 fehlerhaften Schraubprozessen priorisiert. Mithilfe des KI-Systems Analyser®, das auch mit geringen Anlernstichproben auskommt, konnten die Fehlerbilder daraufhin automatisch analysiert und die Ursachen und Maßnahmen je Schraubfall in Echtzeit ermittelt werden.
Die Fehlerbild-Erkennung lief durch die Integration mit dem Prozessdaten-Managementsystem (halb-)automatisch ab.
Ergebnis
50% geringere
Fehlerraten
50% weniger
Nacharbeit
600 T €
gespart in 6 Monaten
Die Lösung
Die vom Analyser® ermittelten Maßnahmen und Lösungen wurden umgesetzt und dieses Vorgehen auf die verschiedenen kritischen Verbindungen in den Werken übertragen. Auch in der Anlauffabrik kam der Analyser® bei geringen Stichproben zum Einsatz und verhinderte die Fehlerraten bereits ab der Null-Serie.
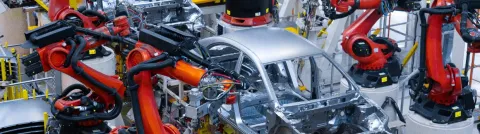
Die Herausforderung
Die Montage von mehreren Spritzgussbauteilen für ein Fahrzeuginterieur ist im Zusammenbau eine Herausforderung bezüglich der Toleranzen, weil sich die Toleranzen und Fertigungsstreuungen addieren. Die Spezifikationen für die Einzelteile mussten daher sehr eng gefasst werden, was bei der Bauteil-Produktion zu hohen Ausschussraten führte.
Das Ziel
Bei der Montage sollte die Rückweise-Rate auf 5 Prozent reduziert werden, auch um Gewährleistungsrisiken zu vermeiden. Zugleich sollten die Herstellkosten gesenkt werden.
Die Vorgehensweise
Mithilfe des KI-Systems Analyser® wurden anhand einer Stichprobe mit 51 Bauteilen nach dem Zusammenbau Vorhersagemodelle für die Montage erstellt. Auf dieser Basis konnten durch statistische Tolerierung und Parametrierung der Prozessparameter die Toleranzen für die Einzelbauteile geöffnet werden, ohne die Qualität der montierten Endprodukte im Zusammenbau zu verschlechtern.
Ergebnis
10% weniger
Herstellkosten
um 30% günstiger
entwickelt
< 5 %
Rückweise-Rate
Die Lösung
Die vom Analyser® errechneten Best Settings mit den weiteren Spezifikationen reduzierten Ausschuss und Nacharbeit sowohl bei den Einzelteilen als auch nach der Montage im Zusammenbau. Die Herstellkosten sanken signifikant, Termine konnten besser eingehalten und Gewährleistungsrisiken gesenkt werden.
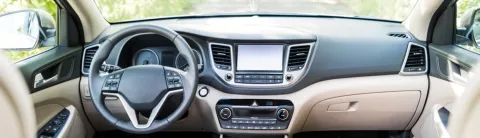
Die Herausforderung
Bei einem OEM im Bereich Optik / Beschichtung mussten die ca. 150 Qualitätsmessgrößen, bestehend aus Einzelwerten und Verlaufskurven, in die Spezifikationen gebracht werden. Einige der Qualitätsmerkmale hatten eine erlaubte Toleranz von nur +- 3 bis 5 µm. Wartungsthemen sollten früh genug erkannt werden, um die Qualität dauerhaft sicher zu stellen und die Wartung vorhersagbar zu machen.
Das Ziel
Die Qualitäts- und Wartungsthemen dauerhaft im Griff behalten, die Wartungsintervalle vorhersagen zu können und den OEE zu steigern waren die Projektschwerpunkte.
Die Vorgehensweise
Aus den ca. 120 möglichen Einflussgrößen und Prozessparametern, vorwiegend Prozesskurven-Verläufe, ermittelte das KI-System Analyser®, das auch Kurven verarbeiten kann, die Wirkmechanismen. Als Stichprobe für die Errechnung der Vorhersagemodelle reichten dem Analyser® ca. 40 Beschichtungsvorgänge aus. Auf dieser Basis konnten die Einflussgrößen und Prozessparameter-Verläufe optimiert und das Best Setting errechnet werden.
Ergebnis
> 320 T€
eingespart /Jahr
99,997%
Yield / Ausbringung
100%
Wartung vorhersagbar
Die Lösung
Mit den vom Analyser® erstellten Vorhersagemodellen und den Best Settings wurden neue Nominalwerte für die wichtigen Einflussgrößen und Prozessparameter-Verläufe ermittelt. Damit konnte sowohl die Qualität auf sehr hohem Niveau bei optimierten Kosten- und Wartungs-aufwänden gehalten als auch der OEE signifikant gesteigert werden.
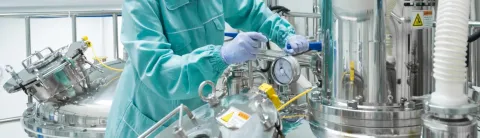
Die Herausforderung
Ein Premiumhersteller für Interieur benötigte zwischen 5 und 8 Validierungsschleifen vom ersten Prototyp bis zur bemusterungsfähigen Serienreife. Die Anzahl der Schleifen ließ sich mit ingenieursmäßigem Ansatz nicht verkürzen, da es für die ca. 150 Qualitätsmerkmale 80 mögliche Einflussgrößen in bis zu 12 Arbeitsgängen gab.
Das Ziel
Neuteile sollten mit nur 2 Validierungsschritten vom Erstmuster bis zur Serienreife kommen. Zugleich sollten das Best Setting für die Werkzeug- und Prozessparameter aller Arbeitsfolgen ermittelt und alle Qualitätsmerkmale nachhaltig ins Ziel gebracht werden.
Die Vorgehensweise
Anhand von gezielten Versuchen errechnete das KI-System Analyser®, das auch mit kleinen Anlernstichproben auskommt, die Wirkmechanismen zwischen den ca. 80 möglichen Einflussgrößen und den ca. 150 Qualitätsmerkmalen aus Geometrie, Oberfläche und Haptik.
Der Analyser® erstellte Vorhersagemodelle, mit denen die Best Settings der Prozessparameter für die gesamte Produktion für alle Qualitätsmerkmale eingestellt werden konnten.
Ergebnis
230 T€
eingespart /Jahr
2 statt 5
Validierungsschleifen
< 2%
Rückweise-Rate
Die Lösung
Mit den vom Analyser® erstellten Vorhersagemodellen und den Best Settings wurden die Nominalwerte für alle wichtigen Einflussgrößen, wie Prozessparameter und Umgebungseinflüsse festgelegt und damit ein Bestätigungslos produziert. Die ca. 150 Qualitätsmerkmale lagen innerhalb ihrer Spezifikationen.
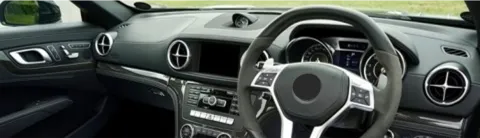
Die Herausforderung
Bei einem OEM erforderten Qualitätsthemen ein Produkt-Reengineering. Aufgrund äußerst komplexer Zusammenhänge zwischen den Prozessparametern und den ca. 160 Qualitätsmerkmalen konnten mit dem üblichen Ansatz die Ursachen nicht nachhaltig abgestellt werden.
Das Ziel
Ziel war es, mit möglichst wenigen Bauteilen die Ursachen der Qualitätsthemen zu analysieren und nachhaltig zu beseitigen. Das Produkt sollte validiert und die Rückweise-Rate dauerhaft gegen 0 % gedrückt werden.
Die Vorgehensweise
Das KI-System Analyser®, das auch mit geringen Anlernstichproben auskommt, ermittelte anhand von ca. 50 Bauteilen das Best Setting für die rund 80 möglichen Prozessparameter und Einflussgrößen. Damit konnten die ca. 160 Qualitätsmessgrößen ins Ziel gebracht werden.
Die anschließende Validierung erfolgte ebenfalls mit Hilfe des Analyser® in einem Bestätigungslos, um das Best Setting abzusichern.
Ergebnis
> 50 T€
eingespart /Jahr
99,98%
Yield / Ausbringung
0,2%
Rückweise-Rate
Die Lösung
Mit den vom Analyser® erstellten Vorhersagemodellen und den Best Settings wurden neue Nominalwerte für die relevanten Prozessparameter und Einflussgrößen ermittelt und das Produkt nach diesem Prozess-Reengineering neu validiert. Damit konnte die Marktstellung signifikant ausgebaut werden.
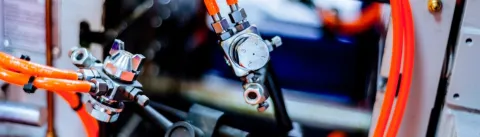
Zertifizierungen
- Six Sigma Black Belt
- Six Sigma Master Black Belt
- Lean Management Black Belt
- Lean Management Master Black Belt
- EFFIMA Berater:in
- BERE Berater:in
mts Consulting & Engineering GmbH
Wernher-von-Braun-Str. 8
82256 Fürstenfeldbruck
Deutschland
Für die Inhalte dieses Expertenprofils sowie die Einhaltung der Urheberrechte des Bildmaterials ist der Profilinhabende verantwortlich.